BDC Systems Ltd, working closely with its long-standing partner Edwards Engineering, has successfully delivered a new grain drying and processing plant for Balgonie Estates Ltd at Southparks Farm, Glenrothes. Balgonie Estates now has a modern, productive and efficient hi-tech plant enabling it to increase the amount of its contract stored grain at the same time as retaining the highest levels of crop quality.
“Our old plant was over 30 years old and we needed to increase capacity and throughput, plus upgrade our drying and processing equipment,” said John Drysdale, MD of Kingdom Farming which manages Balgonie Estates’ farming operations consisting of 1,800 acres of arable and storage contracts with various clients.
“In particular we needed the capacity to manage an increasing amount of oats, not only from our own farms but those deemed as ‘reject crop’ from a local food processing plant,” Drysdale added.
Mr Drysdale approached Edwards Engineering, a multi-discipline engineering firm with more than half a century of experience, to discuss his initial plans for the new plant as Edwards had already successfully installed a Svegma dryer, supplied by BDC Systems, at his own Kilrie Farm.
“Edwards Engineering was restricted to creating the new plant within the existing space of the old plant which would be dismantled. This was a challenge as it required an entirely bespoke design,” explained John Wilson, Area Sales Manager for Northern England and Scotland for BDC, a provider of complete grain plant solutions. “Edwards asked BDC Systems to get involved in the project design right from the initial site meeting.”
Liaising closely with Edwards the design of the new plant was carried out by BDC, addressing changes to the design brief to cater for potential new business opportunities identified by Mr Drysdale and Balgonie Estates.
“BDC has become a very important partner for Edwards over the 20 years the companies have worked together. Largely because of BDC’s ability to offer an extensive range of grain handling solutions as, unlike other providers, it is not constrained by the equipment available from just one manufacturer. This means that together we can deliver solutions that exactly meet the individual requirements of customers,” said Sandy Knight, Edwards’ Agricultural Manager.
Numerous meetings took place and several draft proposals were presented to Mr Drysdale and the Balgonie Estates’ senior management team over a period of 12 months before a final design was agreed.
Designed to dry crops at a higher throughput, the new plant has significantly improved productivity and efficiency; it consists of a large bunker area with a below ground 16m long trench intake conveyor from where the grain is transferred into the plant.
The grain is handled throughout the new plant by ten Skandia Elevator H-Line 80tph conveyors and six Skandia H-Line elevators.
The grain’s journey continues through the plant via a Cimbria pre-cleaner. From there the grain is transferred outside to the BDC Svegma continuous flow 50tph dryer fitted with vertical turbo clean dust extraction fans, with any overflow returned to the intake bunker. Once dried, the grain returns to the plant through a small BM Silo buffer bin and feeds a Cimbria fine cleaner before being transferred to the floor store buildings.
All the equipment within the plant is connected to a JKF dust filtration system which removes all of the dust from the crop to a trash storage building.
“At the heart of the new plant is a BDC hi-tech PLC control panel that enables just one person to manage the entire plant from the control room,” said Mr Drysdale. “All the slides and valves throughout the plant are motorised so the plant manager, using the touchscreens on the control panel, can select the required grain routes.”
The automated control panel allows the plant to continue to work if the manager is offsite. Crucially, blockage probes, rotation sensors and belt alignment switches fitted to the grain handling equipment, close the plant down if activated. The manager is immediately alerted via text or email and so is able to deal with any issues without delay.
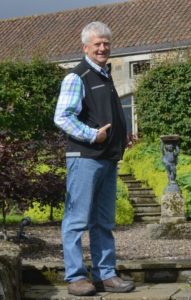
John Drysdale
“As well as increasing its overall drying capacity by 50% and improving the cleaning and dressing of the grain, Balgonie Estates is now able to dry high moisture oats and wheat from +24%mc down to storage moisture of 12%mc and to dry crops, including those from sources other than its own farms, down from 15%mc to 12%mc,” added BDC’s Mr Wilson.
“BDC and Edwards have a fantastic partner relationship. This meant that I had complete confidence that the grain handling equipment they recommended would provide the best possible solution for Balgonie Estates with no compromises on what we really needed,” said Mr Drysdale. “Between them they managed to successfully deliver our somewhat complex and changing requirements for a completely bespoke grain drying and processing plant that has not only met but exceeded our expectations, on time and on budget. You can’t ask for anything more!”